ASCMO-MOCA (Model Calibration)
ETAS ASCMO-MOCA enables the optimization of parameters in physics based models like the ones used in the ECU and simulation environments. Various plant models and controller models can be loaded, connected, or modeled for this purpose. It is furthermore possible to load measurement data, import and export model parameters, and define optimization tasks. ASCMO-MOCA provides a wealth of functions and options for visualizing and analyzing the data as well as the models used. Powerful algorithms are able to optimize a large number of free parameters simultaneously while taking into account constraints like smoothness or monotonicity.
A very common use for ASCMO-MOCA is in the optimization of the prediction quality of ECU models (virtual sensors) for e.g. torque or exhaust-gas temperature. With this, the deviation of the model prediction from a real measurement on the engine test bench or in the vehicle is minimized for all measuring points.
Another application is the optimization of emissions and fuel consumption for complex internal combustion engines in dynamic/transient driving cycles. This requires linking classic ASCMO data-based models to parts of the ECU software. Such linkages and the joint optimization of different subcomponents are very straightforward in ASCMO-MOCA.
Since the methodology used in ASCMO-MOCA is not tied to the internal combustion engine, the tool is also used in areas like electric mobility (e.g. charging strategy) and component development.
Benefits
- Easy to use with no specialized knowledge required
- Support for common model formats like ASCET, Simulink, and FMI/FMU
- Flexible option for freely reproducing functions as formulas and for linking models
- Interactive graphical representation of data and results
- Powerful optimization methods
- MATLAB® and COM interfaces for remote control and the integration of customer-specific functions
Features and Functions
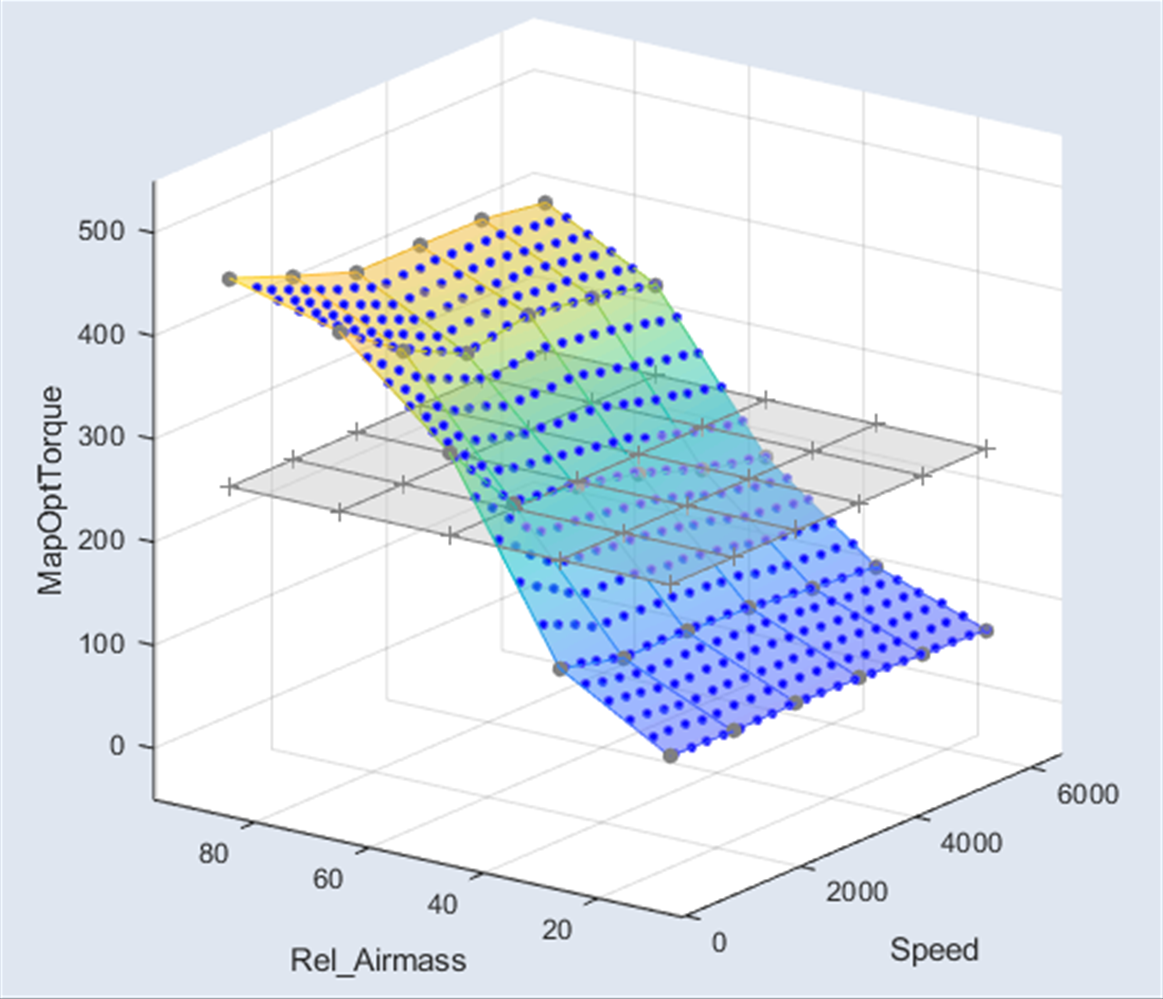
ASCMO-MOCA can read various common file formats. Multiple data sets can be loaded into the tool and weighted differently for later optimization. The individual channel names used in the measurement files can each be assigned to the name used in the models. This means that once a project has been created, it can be reused with new data sets containing different names without having to modify it. The measurement channels can be conveniently converted to handle the different units.
ASCMO-MOCA provides a wide range of visualization options for checking the plausibility of the data and results. They can take the form of interactive scatter plots or time-based scope views. Once views have been selected, they can be stored as templates and used again later on for new data sets and analyses.
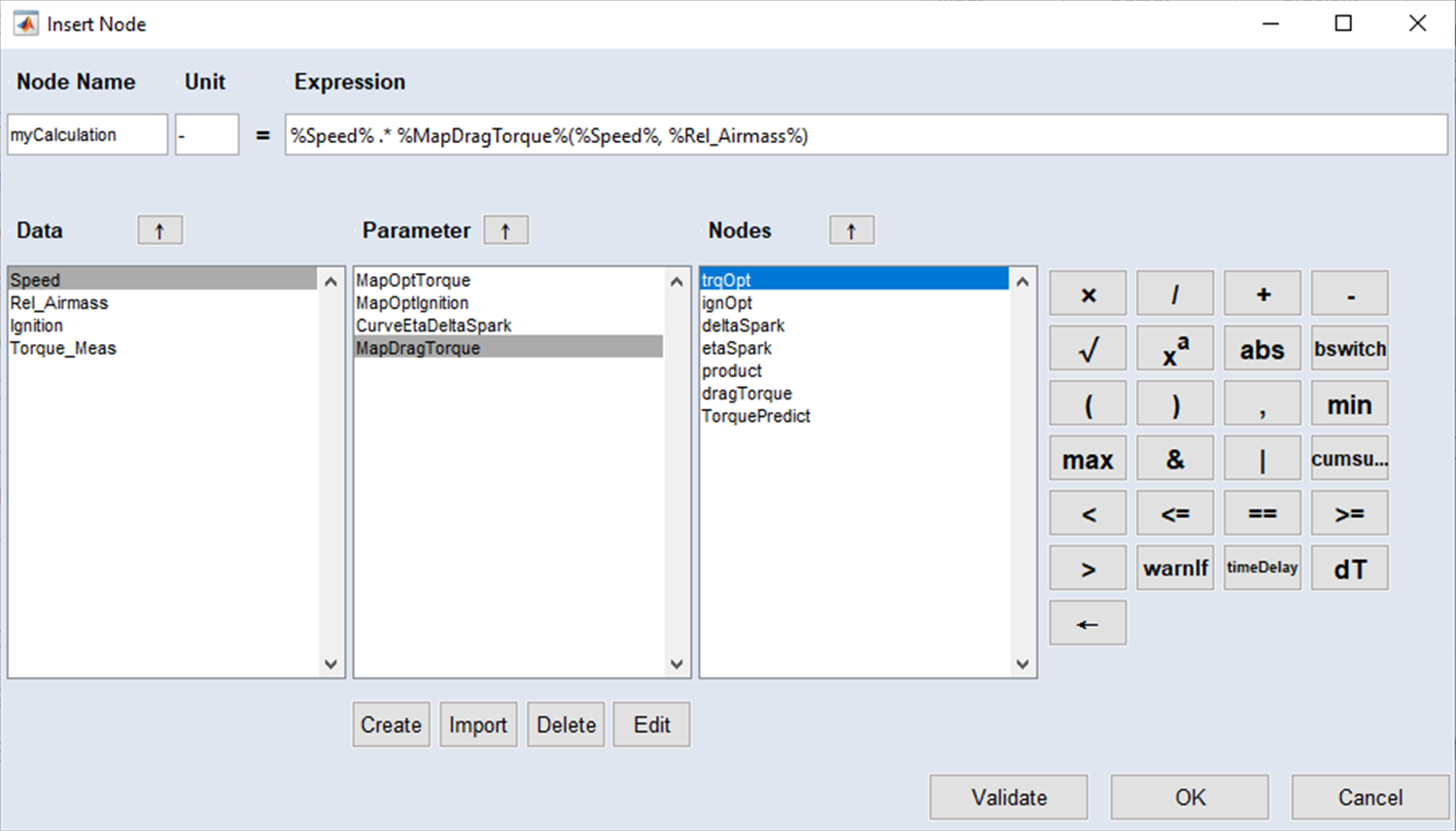
An essential step in ASCMO-MOCA is to provide the tool with the relevant models.
In principle, it makes no difference whether the models are going to be used as pure plant models or as controller models containing parameters that are going to be adjusted and optimized. ASCMO-MOCA supports the following common model formats: Simulink, FMU, ASCET, TSim Plugin, COSYM Simulation and ASCMO-STATIC / ASCMO-DYNAMIC. With support provided by ASCMO-MOCA’s automatic model analyses, each model is configured separately so it can access the respective inputs and outputs and, if available, internal parameters. An important aspect when it comes to the Simulink models is that the models are executed directly within the Simulink environment. Within Simulink, there is therefore a high degree of independence from the versions and functionalities used.
ASCMO-MOCA makes it possible to link several of the above-mentioned models with one another using freely definable formulas. Moreover, the formula language provides users with a universal way to directly rebuild the model structure that they want. This is needed particularly when no finished models are available or if they cannot be accessed. Another significant advantage provided by this formula based option is the extremely high optimization speed. A formula editor simplifies the task of entering the formulas by, for instance, supplying the user with all of the already existing measurement channels, parameters, and model outputs as well as standard arithmetic operations.
ASCMO-MOCA makes it easy to create, manage, and edit the parameters of the models, which generally exist in the form of characteristic maps, characteristic curves, and scalar values. The user can import or export parameters in common formats as well as create completely new parameters. The parameters are each displayed in a suitable form, such as in characteristic maps. They can be changed graphically using the mouse or by entering values in tables using the keyboard. The tool also allows upper/lower limit values and reference values to be defined for each parameter.
ASCMO-MOCA provides a convenient way of managing various sets of parameters. There is always a so-called current working set as well as a reference set. Further sets can be defined and named by the user in addition to these.
Moreover, during the optimization process, several parameter sets are saved automatically. Every iteration as well as each version before and after the optimization is saved as an additional parameter set.
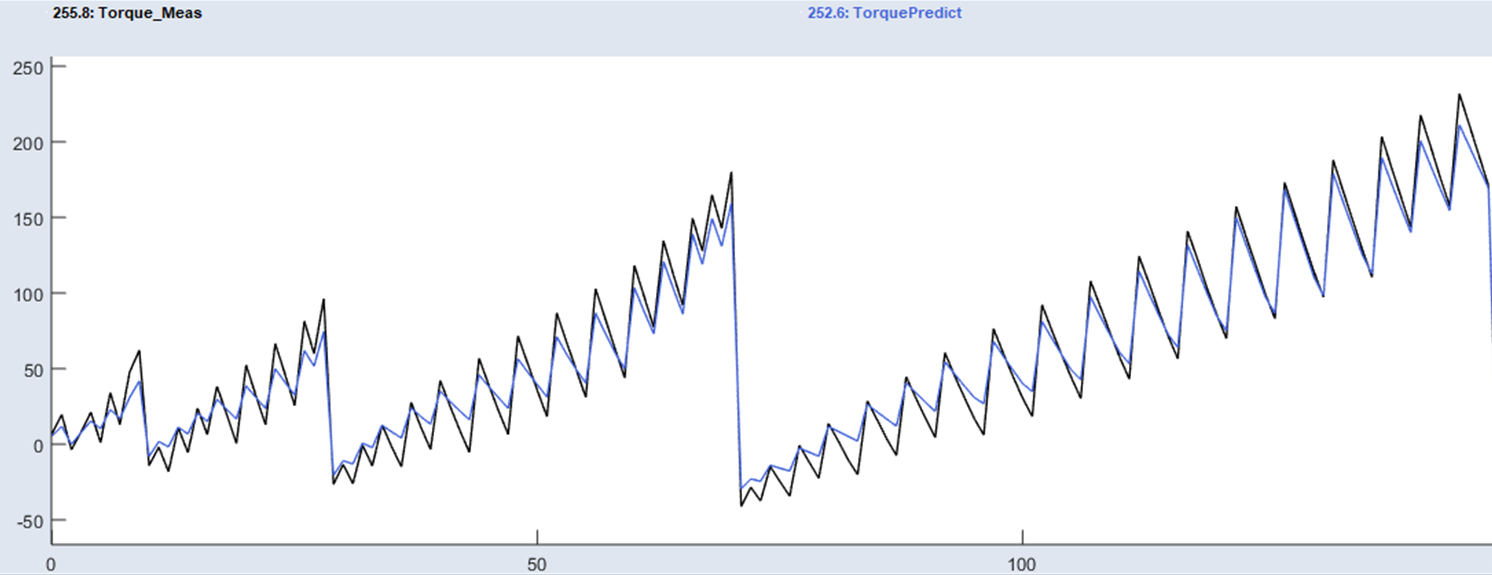
ASCMO-MOCA’s primary task is the optimization of model parameters. This usually involves comparing the calculated output of a model with a real measurement. The deviation between each individual measuring point and the model prediction is then used as a measure for judging how good the correlation is. The root-mean-square model error (RMSE) is calculated and displayed for this purpose. The optimizer then minimizes the RMSE by varying all the free parameters.
In addition, a wide variety of freely definable boundary conditions can be taken into account in the optimization:
- Definition of the range within which a parameter may be adjusted
- Smoothness of characteristic maps or curves or their gradients and monotonicity
- Several optimization criteria simultaneously, including their weighting
- Exclusion of individual characteristic map or curve values from the optimization
It can be useful for several reasons to divide the optimization into multiple sub-steps (sequencing). This can lead to the optimization goal being reached more quickly or can result in the parameterization of the models (combination of parameter values) being influenced in such a way that it better corresponds to the expected physical dependency. Typical functionalities related to this are:
- Selecting the parameters to be optimized
- Changing the number of break points of characteristic maps and curves
- Changing the weighting for data sets or optimization criteria
- Adapting the upper/lower limits and smoothness
- Selecting subsets of the measurement data
ASCMO-MOCA provides a range of statistical analyses and visualizations for analyzing the optimization results in detail. The error distribution before and after an optimization can be displayed, for example, in the form of a histogram or any combination of point clouds. In addition, the tool also offers sensitivity and correlation analyses.
Compatibility
ASCMO-MOCA is open and flexible. The tool supports all relevant data formats that are used, for example, in the ECU software and in calibration. Using the MATLAB® interface, it is possible to easily integrate customer-specific functionalities and adaptations and automate operations with scripting.