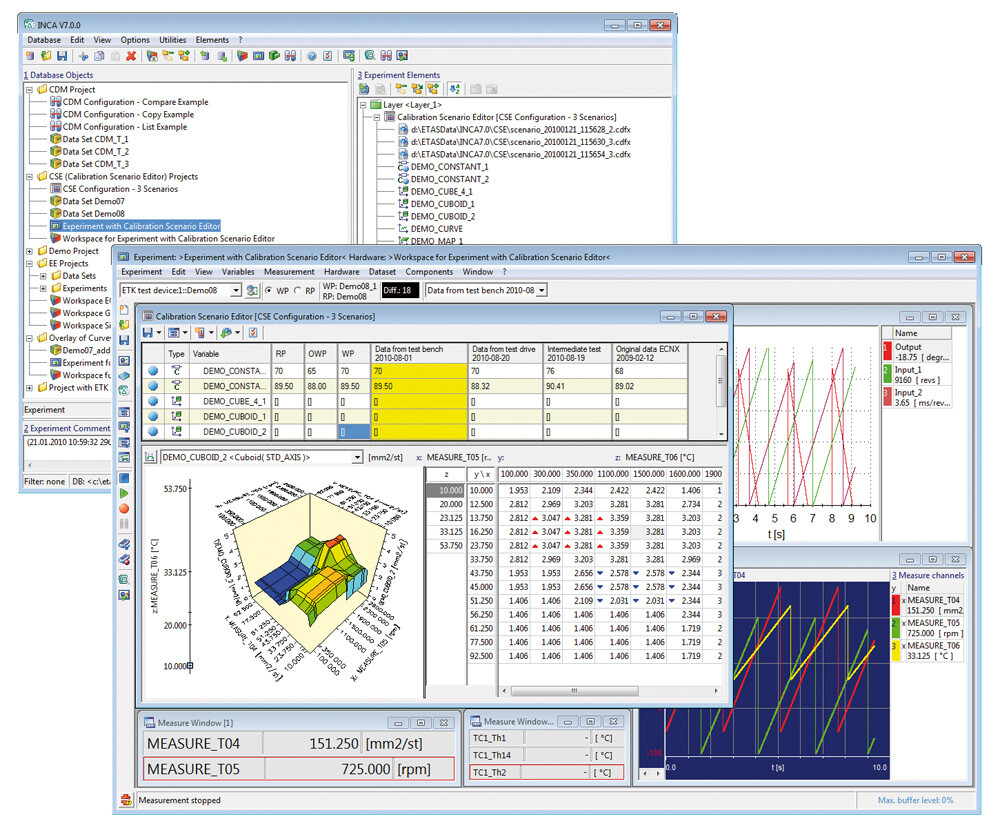
The numerous innovations and improvements of the new version 7.0 increase the efficiency and performance of the tools while also offering new possibilities for integrating tools and data in the development environment of the customer.
Standards and open interfaces
For the seamless integration into the development environment, INCA comes with a number of open interfaces. INCA V7.0 is compliant with the new specification for exchanging measurement data, ASAM MDF4, and with the latest versions of the ASAM standards MCD-2 MC (ECU description for measurement and calibration systems) and MCD-3 MC (test bench interface). INCA V7.0 is the only tool currently on the market which supports the parallel connection to automation and auto-optimization on the test bench according to the ASAM MCD-3 MC V2.2 specification.
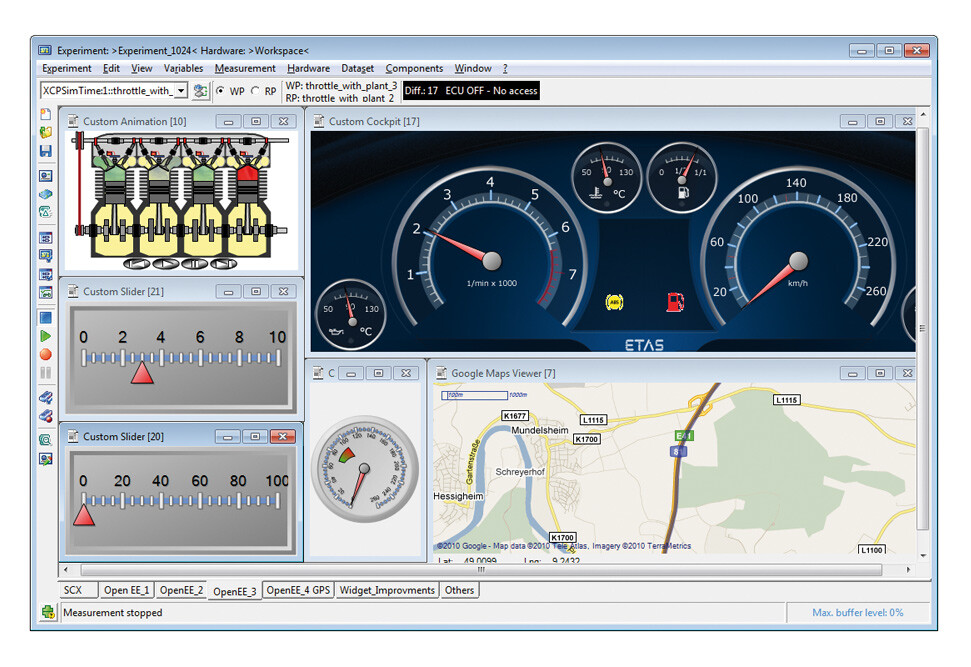
The new Instrument Development Kit allows the extension of the INCA experiment environment with proprietary control and display elements. The supplied instructions, examples and a configuration wizard facilitate the development of specific instruments for the user.
In INCA V7.0, the mechanisms for integrating in-house or third-party hardware have been expanded. It is now possible, for example, to use measurement value catalogs with integrated third-party hardware. INCA V7.0 supports the documentation of calibration data with a new generic interface which allows the easy generation of customized file formats and layouts. The new eCDM interface to the enterprise calibration data management allows the exchange of calibration data directly between INCA and data base systems.
Sharing one configuration
With INCA V7.0 it can always be ensured that the work in a project or a department is done on identically configured INCA computers. In the new INCA version, the settings of the user options can be adjusted quickly and easily between different PCs. Differences in the user options on different PCs can be identified quickly. When installing INCA V7.0, the existing settings can be taken over automatically from the previous version.
The quick way to the optimum experiment

The configuration dialog of the INCA experiment environment has been completely revised in the new version. The new dialog allows the direct configuration of control and display elements of the experiment when selecting the calibration values and measurement signals. Existing INCA experiments can be easily and quickly adapted using the new dialog. The multiple selection option enables the quick and consistent configuration of display settings of different labels.
-
Video: Introduction to the INCA Variable Selection and Experiment Configuration Dialog Download

The new Virtual Device for ECU interfaces facilitates the preparation of experiments without connected hardware in the office. The advantage: The settings for the acquisition of ECU signals do not have to be reconfigured in the vehicle. In addition, the handling of master/slave ECUs is straightforward in INCA V7: ECUs can be grouped already in the data base browser. In the experiment, it is possible to select the parameters for the ECU group or the individual ECUs in the group.
Graphical comparison of characteristic curves
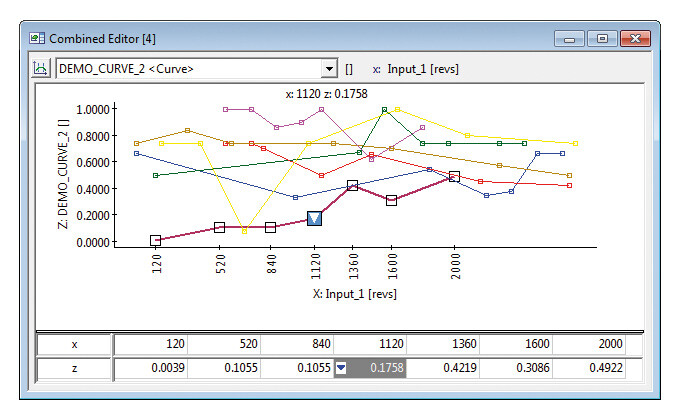
INCA V7.0 extends the functionality of the combined calibration editor. In the new version of the editor, the characteristic curves can be superimposed for a quick visual comparison. Changes to the individual characteristic curves can be performed as usual in the table view or directly in the graphic chart using keyboard or mouse.
GPS-synchronous measurement data
During a test drive, INCA V7.0 lets you capture position data using a GPS mouse synchronously to the acquisition of ECU data. GPS data can be exported and stored separately for the display in electronic maps such as maps.
New hardware options
INCA V7.0 offers complete support of all interfaces of the modules ES910, ES920 and ES921, so that they can be used for ECU function development, for measurement and calibration in the vehicle as well as in a real time interface between the ECU and the test bench. INCA V7.0 also supports the new two-channel version of the USB CAN bus module ES581, and the new ECU and bus interface modules ES592, ES593-D and ES595.
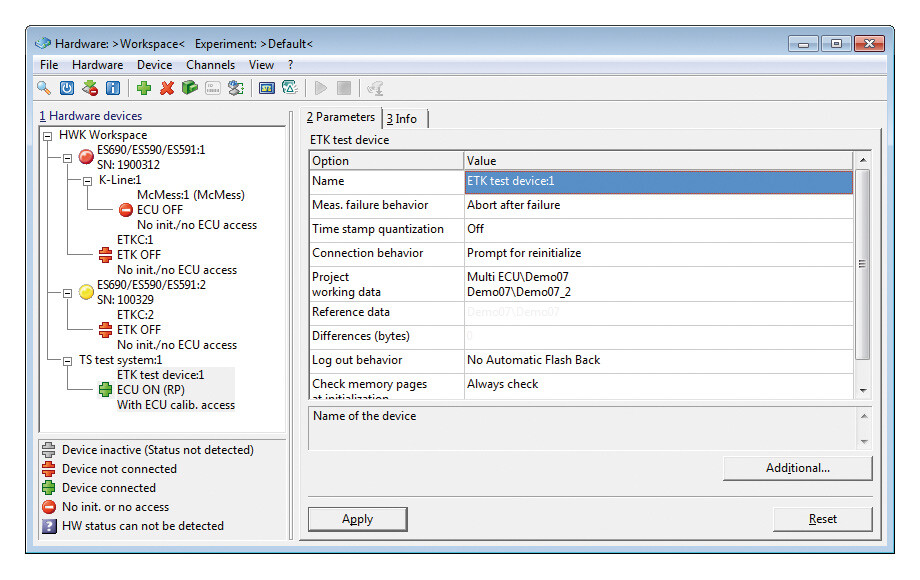
To ensure the function of the overall system, INCA V7.0 automatically controls whether the hardware is programmed with the corresponding firmware when hardware is connected. Necessary firmware adaptations can be easily made directly in INCA.
Hooks for the ECU
The new EHOOKS tools from ETAS provide ECU function hooks for development and calibration purposes quickly and in high quality. The new INCA add-ons EHOOKS-CAL and EHOOKS-BYP allow simple activation or deactivations of hooks in the ECU for looping in parameter values using INCA or for bypassing of functions.
Easy integration in the tool and ECU environment
For connecting ECUs via CAN or Ethernet to INCA, ETAS provides the Integration Package XCP-IP free of charge. XCP-IP contains source code for the XCP ECU driver, a comprehensive documentation, and a configuration tool. The XCP-IP driver supports ECU measurement, calibration, flash programming and bypassing.
With the MDF-IP Measure Data Format Integration Package ETAS provides a software module that lets other tools read and interpret measurement data. MDF-IP ensures a seamless exchange of INCA measurement data in the development and calibration process.