High-performance prototyping target for computationally intensive bypass applications
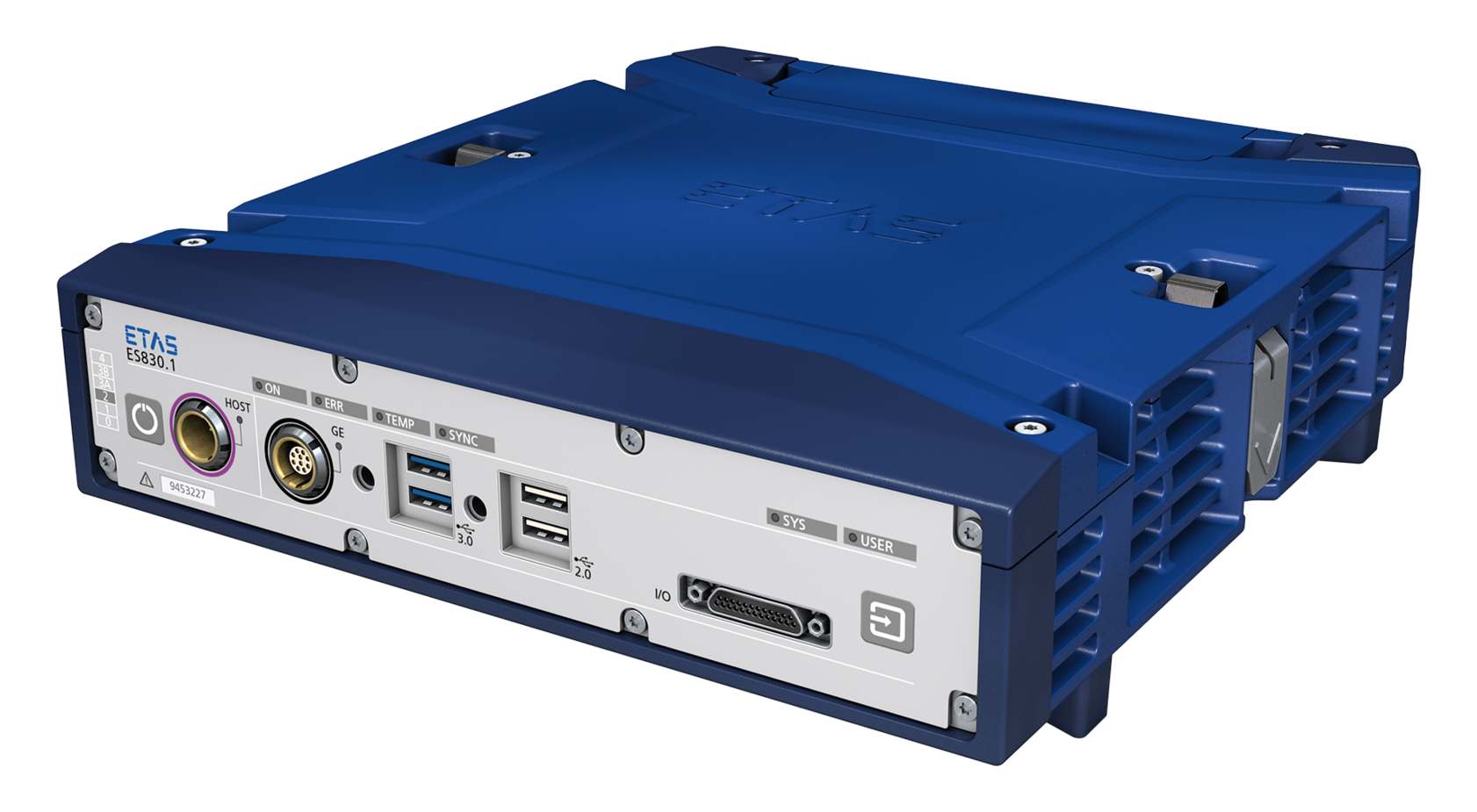
The ETAS ES830 Rapid Prototyping Module is a high-performance experimentation platform for the development and validation of ECUs and electronic vehicle systems – both in the laboratory and in the vehicle. As a component in the ES800 product family, it enables developers to run multi-ECU and multi-controller applications in combination with one or more simulation models without first having to adapt the ECU software or carry out complex and time-consuming coordination processes with ECU manufacturers.
A significant benefit is that rapid prototyping of ECU functions as well as measurement and calibration tasks can all be performed on the ECU in parallel. Equipped with a multi-core processor, the ES830 ensures low latency and jitter for the bypass applications. The ES830 communicates with up to three ECUs via ETK as well as via the CAN/CAN FD, FlexRay, or LIN vehicle buses.
Through validation of the modeled software functions in real time and under real conditions using the ES830, development quality is increased and the development time as well as the costs are reduced.
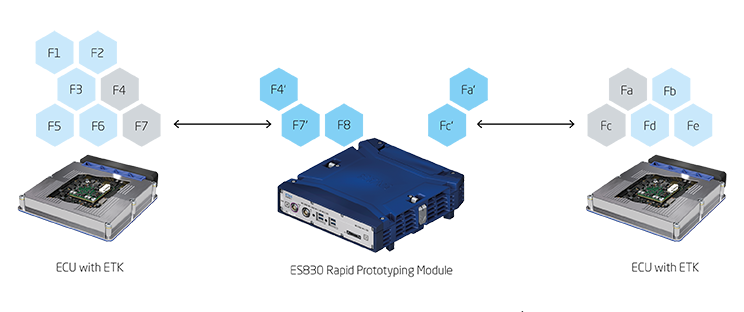
Important functions
- Prototyping target equipped with an Intel© Core™ i5 processor for computationally intensive bypass experiments with up to three ECUs simultaneously
- In combination with the ES800-family interface modules, a whole range of interfaces is available: ETK-S2x, XETK, FETK, Ethernet, FlexRay, CAN/CAN FD, LIN, two Gigabit Ethernet ports, and an I/O connector for querying status information
- The ES830’s multi-processor architecture ensures that the performance impact due to bus and bypass communication is minimal
- The automotive operating system from the ETAS RTA family enables a smooth transition from the finished function prototype to the production-ready ECU software
- Configuration options for wake-up and logging via web GUI for any browser
Areas of application
- Function development in research, advance engineering, and production development
- Testing of control and diagnostic functions under real conditions in the laboratory, on the test bench, or in the vehicle in all phases of development
- Replacing real components with virtual hardware from simulation models
- Computationally intensive bypass and fullpass applications for the development and optimization of vehicle functions
Main Benefits
- Realistic testing using high computing power and simulation performance with low latency and jitter
- Now just a single piece of hardware for multi-ECU and multi-controller applications in combination with one or more simulation models
- Future-proof thanks to numerous interfaces and expandable stack design
- Suitable for vehicle testing involving harsh environmental conditions thanks to robust construction
Usage with other ETAS products
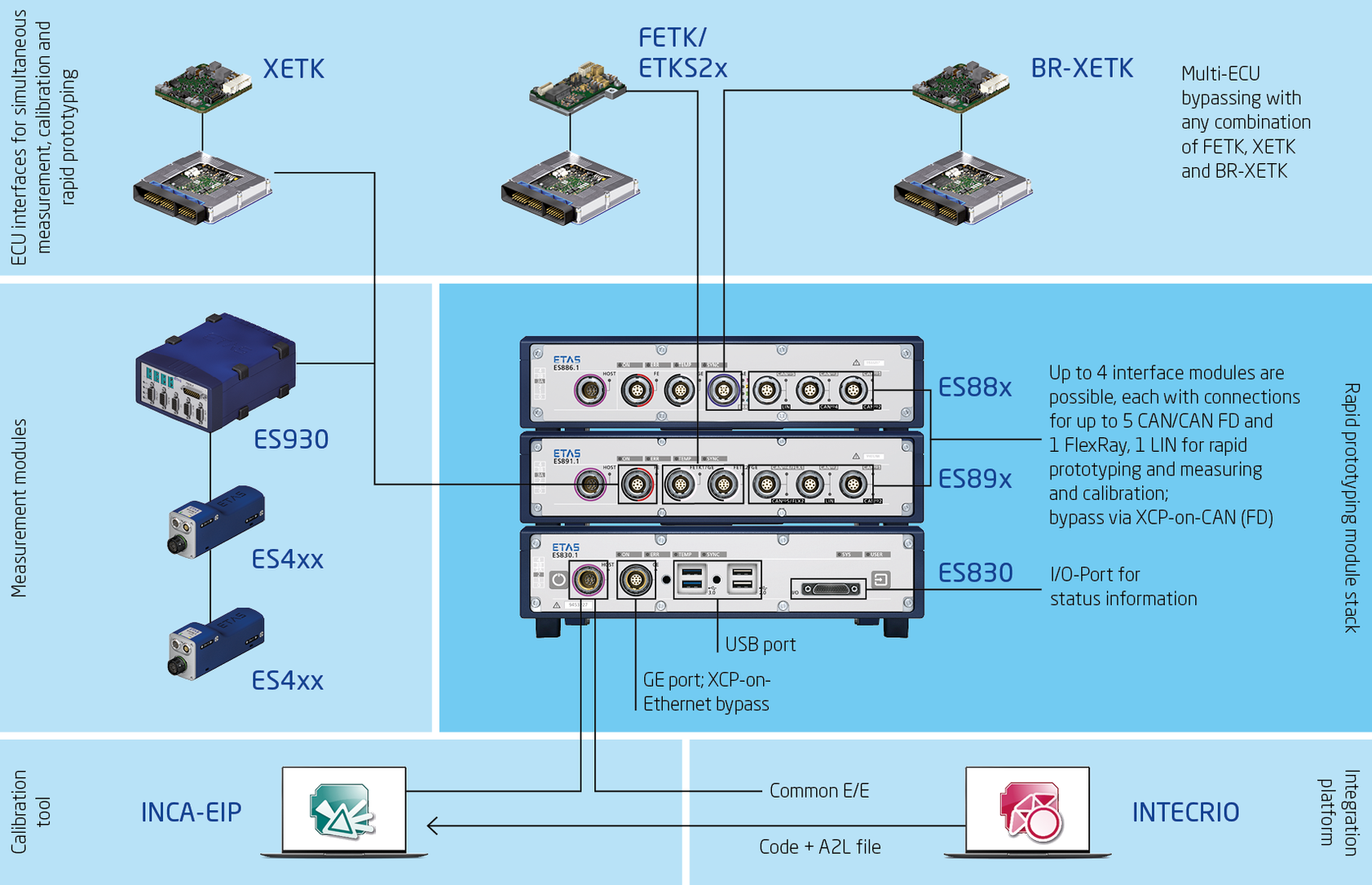
The ETAS ES830 rapid prototyping module is a component of the ETAS prototyping solution.
With ETAS EHOOKS, developers can insert bypass hooks without any knowledge of the software details directly into the HEX and A2L files of the existing ECU software. No access to the source code or the ECU software build environment is necessary for this. Function prototypes developed with ETAS ASCET or MATLAB®/Simulink® are then integrated with a high degree of flexibility using ETAS INTECRIO and the bypass is configured. The connection between the ECU and the ES830 is established by means of an ETK ECU and bus interface module from the ES890 product family and the appropriate ETK. The ES890 also provides the connection to the vehicle buses and the ETAS measurement technology. The validation of the new control, regulating, and diagnostic functions takes place via ETAS INCA under real conditions, in real time, and with low latency.
The ES830’s multi-processor architecture ensures that the performance impact due to bus and bypass communication is only minimal. The operating system from the ETAS RTA product family ensures a smooth transition from the finished function prototype to the production-ready ECU software.