Benefits
- Acquisition of tens of thousands of signals from the ECU at high cycle rates by means of the new FETK interface
- Connection to several FETK ECUs plus CAN, CAN FD, LIN, or FlexRay vehicle busses in parallel by new ES89x ECU and Bus Interface Modules
- Easy centrally controlled, automated INCA installations by using Windows Installer
- Support of Windows 10
The flexible software tools in the ETAS INCA product family are designed for electronic control unit (ECU) calibration and diagnostics and to record ECU measurement data. As INCA was developed further, new functions were provided quarterly in the form of service packs from version 7.1 on. All these functions are contained in INCA V7.2. In addition to the Microsoft Windows® Vista* and Windows® 7, 8, and 8.1 operating systems, the new version also supports Windows® 10.
* Support up to INCA V7.2 Service Pack 4
Recording large volumes of ECU data
Used in conjunction with the ETAS FETK-T interface for high-performance control units and the new ES891/ES892 interface modules, INCA V7.2 allows users to record data at high cycle rates. During measuring trips, more than 56,000 different variables can now be simultaneously captured and recorded from the ECU.

Acquisition of data from the ECU through the FETK interface:
FETKs are offered in two versions: FETK-S (bottom left) and FETK-T (bottom right).
Both variants use a microcontroller-specific production device (µC-PD) debug interface such as JTAG (Joint Test Action Group), DAP, or LFAST as control access. Additionally, T-type FETKs support the particularly powerful µC emulation device (µC-ED) trace interfaces, along with the high-performance transmission of trace data from the ECU over the serial Aurora interface.
The comprehensive measurements can be saved in compressed form in ASAM MDF V4.1 format without loss of quality, which allows file sizes to be reduced by up to 60 percent. For fast inputting of data, the measurement files can be indexed, and INCA V7.2 supports MDF-compliant indexing. In conjunction with the MDA measurement data analysis tool, a proprietary indexing system is also offered as an alternative, one that allows very large measurement files to be input quickly into MDA.
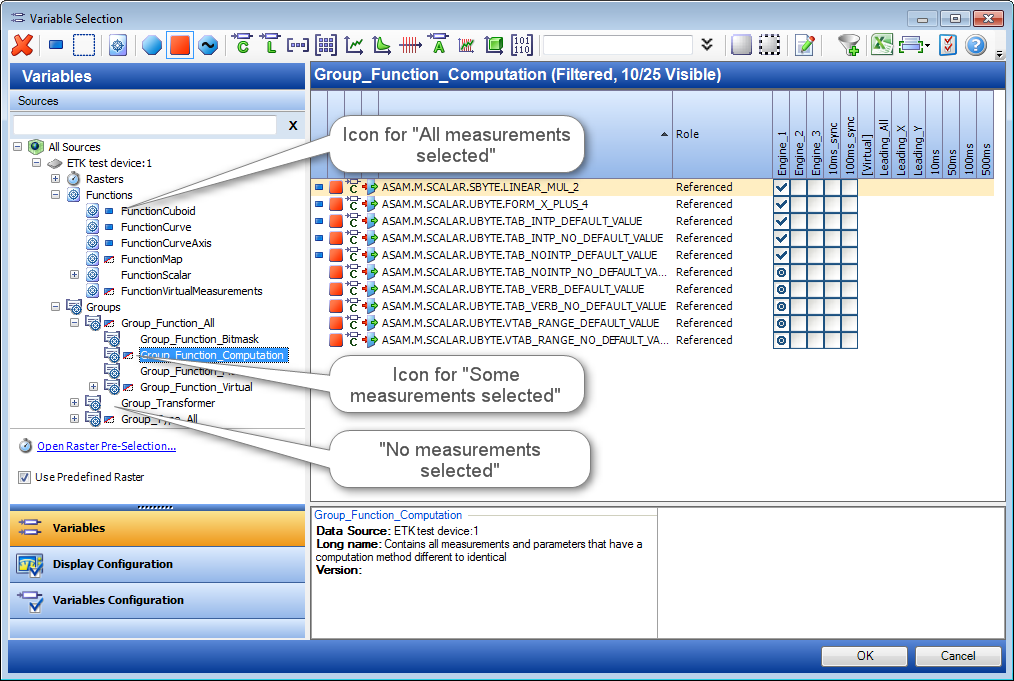
To facilitate the quick preparation of measurements with many variables, ETAS has speeded up the loading of extensive experiments and the opening of the variable selection dialog. In addition, the mechanisms for selecting variables were expanded to allow users to quickly and easily select many signals and assign measurement rasters. For example, users can select measurement variables for a function or a group as a block.
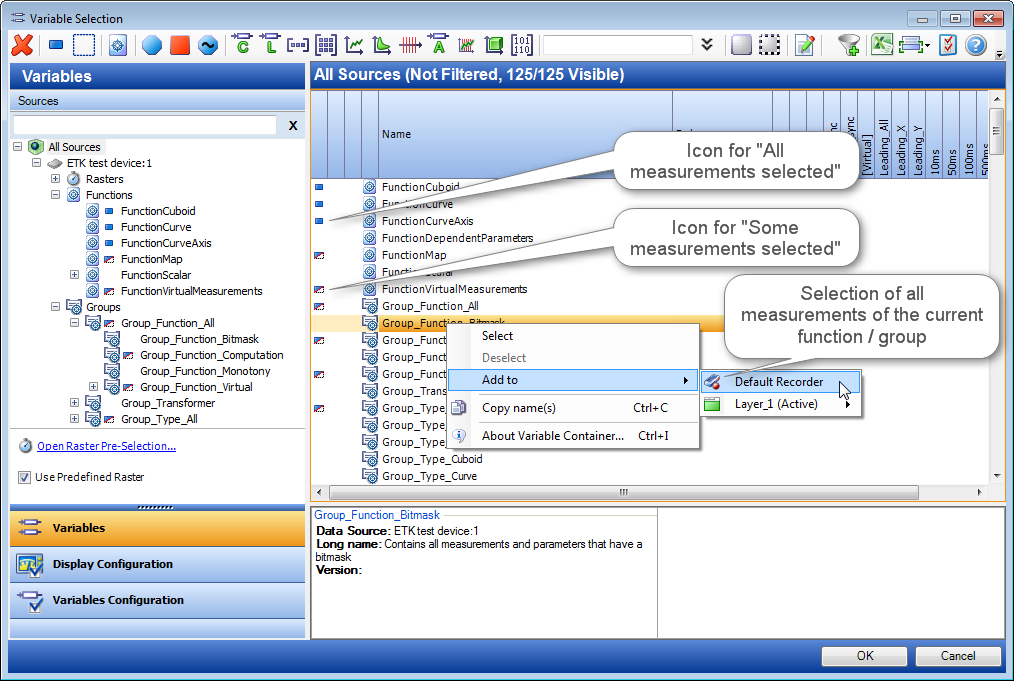
Conversely, the variable search function was augmented. Now the windows in an experiment that contain the searched variable are visually highlighted. If a variable is not found, the user can switch directly from the search to the variable selection dialog. When this happens, the search filter is adopted automatically.
What’s more, the display quality of experiments was improved and the whole experiment environment features greater screen contrast. The frames of active display windows are color-highlighted, whereas the colors of inactive displays match the background. In inactive windows, the control fields are hidden so that window names can be displayed more effectively.
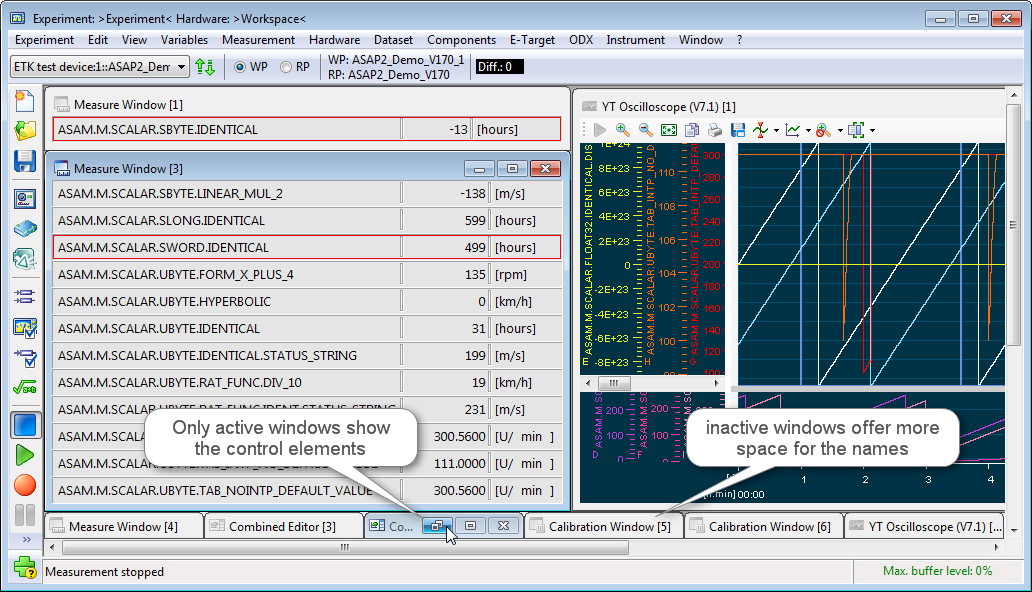
To optimize the area ratio of measurement display and legend for virtual oscilloscopes, users can adjust the font size in the legend between 6 and 14 points. And to make binary measurement values easier to read, 4-bit number sections in the display are separated by spaces.
Calibration data and quality management
INCA’s CDM (Calibration Data Manager) enables users to choose among various options with respect to accuracy when comparing different ECU data. With INCA V7.2, users can carry out the comparison with an accuracy that can be stored in the corresponding ASAM A2L file. When comparing data records with different accuracy specifications, the highest is used. In A2L ECU description files, the upper and lower limits for characteristic values can be specified, which can now be optionally checked by INCA when importing calibration data. Alternatively, the check can also be carried out for already imported data.
When exchanging calibration data using data management systems such as AVL CRETA, calibration values are now taken directly from the ECU HEX files and no longer stored separately in CDF description files. That increases the data exchange rate by between 20 and 30 percent. The INCA-QM-BASIC (Basic Quality and Maturity Tracking) add-on now supports metadata for process description, such as statistical information or comments that can be left in CDF files. Users can display, edit, and filter the metadata in the CDM (Calibration Data Manager).
Use on the test bench
Using the INCA-MCE (Measurement and Calibration Embedded) add-on for the ES910 Prototyping and Interface Module and INCA, a real-time connection can be established between test bench and ECU. INCA-MCE now also supports ECU measurement rasters containing signals with a total length of more than 1,024 bytes. During the configuration of the ES910 module, all measurement and calibration variables of an INCA experiment can now be added automatically. In addition, as with INCA, ETK ECUs with limited calibration RAM can be calibrated. For this purpose, the RAM can be managed either by INCA or by the user. Accordingly, when preparing experiments, the calibratable variables can be either suggested automatically by INCA based on defined criteria or selected manually by the user. To maximize the number of variables available in the RAM, memory space that is no longer required is automatically freed up.
Because the expanded ASAP3 interface supports the new EXTENDED_GET_PARAMETER and EXTENDED_SET_PARAMETER commands, ASCII and 32-bit integer data can be transferred. This means, for example, that the ECU software version or status information can be communicated to the test bench. Independently of this, the characteristic values that are displayed in an experiment’s editors are now updated automatically even when they are changed remotely via ASAP3 or COM-API (Component Object Model API).
New interface options
As well as supporting the new FETK interfaces and ES89x modules, INCA V7.2 offers numerous other attractive hardware options. With the new ETAS ES583 module, a handy pocket-sized USB FlexRay interface is available for INCA. Then there is its counterpart, the ES581.4 USB-CAN interface module, which now allows both channels to be used in parallel by two applications, such as INCA and BUSMASTER.
For processing the high-precision positional data of the modern GALILEO and GLONASS global navigation systems, INCA V7.2 supports the extensions of version 4.1 of the NMEA 0183 standard for global navigation satellite system (GNSS) receivers.
For CAN FD applications, the ES523, ES891, and ES892 ECU and Bus Interface Modules are available for bus monitoring and for calibration and diagnostics using the XCP-on-CAN FD and UDS-on-CAN FD protocols. In addition, INCA now also supports LIN-V2.2 and SAE-J2602-LDF files for monitoring signals transmitted on LIN buses. The monitoring of J1939 CAN signals is possible with INCA V7.2 for data rates of 250 kBaud and 500 kBaud. J1939 signals, which use CAN messages’ 29-bit identifier for coding and multiplexing information, are treated as conventional measurement signals during INCA operation, such as when users select variables.
ASAM MCD compliant
With the transformer mechanism, which is specified in version V1.7 of the ASAM MCD-2 MC (ASAP2) standard, INCA V7.2 can display complex ECU program calibration objects in an application-optimized form. To this end, the ECU software manufacturer provides specific transformations in the form of a DLL (dynamic-link library). In addition, the new INCA version supports multi-dimensional characteristic and measurement variable fields. The field dimension here is stored in the A2L file using the new ASAM MCD-2MC keyword “MATRIX_DIM”. When calibrating function models, it makes sense to map the names of model parameters to the designations of the corresponding characteristic variables in the ECU. For this purpose, INCA supports the new ASAP2 keyword “MODEL_LINK” in A2L and CDF (Calibration Data Format) files.
INCA V7.2 supports the first parts of the new version 1.3 of the ASAM MCD-1 XCP communication protocol, including the new XCP-AML for A2L files and error correction in accordance with the new XCP error codes on CAN, CAN FD, FlexRay, and Ethernet transport layers. As an alternative to measuring variables that are stored in data acquisition (DAQ) lists, measurement data can now also be recorded by CCP (CAN calibration protocol) and XCP ECUs in polling mode. To do this, INCA cyclically reads in data that the ECU writes to addresses to which the respective measurement variables are assigned. As an extension to the DAQ-based measurement method, INCA provides improved formulas for calculating computing load and the RAM requirements of dynamic measurement raster tests even for multi-core ECUs.
As well as supporting ASAM standards, INCA can now also process descriptions of CAN and CAN FD networks that are compliant with AUTOSAR Release 4.1.
ECU flash programming
From version V7.2 upward, INCA can now also program ECU flash memories using UDS (Unified Diagnostic Services) via FlexRay and via XCP over Ethernet. In the ProF scripts that INCA uses for programming, the delay period for the deletion of existing memory content, for which XCP specifies a value of around 65 seconds, can now be configured by the XCP command “PROGRAM_CLEAR”.
For flash programming binary files in the Motorola S19 format, INCA now supports the S6 3‑byte data format as well as the S5 2-byte data format. Transmitting larger blocks of data shortens the programming times.
For comparing individual bits of variables, the operators AND, OR, XOR, and NOT can now be used in ProF scripts. To suppress the communication of ECUs on the CAN bus, INCA can send specific CAN messages with a random CAN ID before and during the programming operation. The ProF commands for sending CAN messages can now also be used when programming via CAN FD.
ECU diagnostics
The ODX-LINK add-on to INCA V7.2 supports the worldwide harmonized onboard diagnostics standard WWH-OBD (ISO 27145), which applies primarily to commercial and heavy goods vehicles from model year 2014 on in the Euro VI emissions class. All WWH-OBD data can be requested by ECUs, displayed on instruments in the test environment, and recorded and stored by INCA in MDF files.
In addition, the new ODX-LINK version makes it possible to use the new error codes in accordance with SAE J1979-DA and SAE J2012 as well as description files in PDX, ODX, or XPRJ format and the ODX command COMPARAM in accordance with ODX V2.2 (ISO/DIS 22901-1) for initializing devices via KWP2000-on-CAN or K-Line and UDS-on-CAN. On account of their compatibility with ODX V2.2, it is possible to continue using ODX V2.0.1-compliant INCA projects with ODX-LINK and ODX-FLASH.
MSI installation and Simulink® integration
INCA V7.2 can be set up either on its own or in parallel with version 7.1 of the software. The installation routine is now based on MSI Windows Installer technology, which makes it much easier to have a centrally controlled, automated rollout of the software. With the aid of the MSI routine, users can select, configure, install, and uninstall the required INCA software tools in one step, while the routine verifies the compatibility of the versions of add-ons and basic installation. In the process, the named-machine, named-user, and floating license variants, as with other INCA products, are now also offered for the INCA-LIN (LIN Integration Package) and INCA-FLEXRAY add-ons.
The functionality of the INCA-SIP (Simulink® Integration Package) add-on, which enables users to record and change parameter values from MATLAB®/Simulink® models while a simulation is running in INCA, is now included in the INCA-EIP (Experimental Target Integration Package) add-on and will be provided to all INCA-EIP users without additional costs.