Herausforderung „Antrieb der Zukunft“
Test und Validierung von Brennstofzellen-Steuergeräten erfolgreich meistern
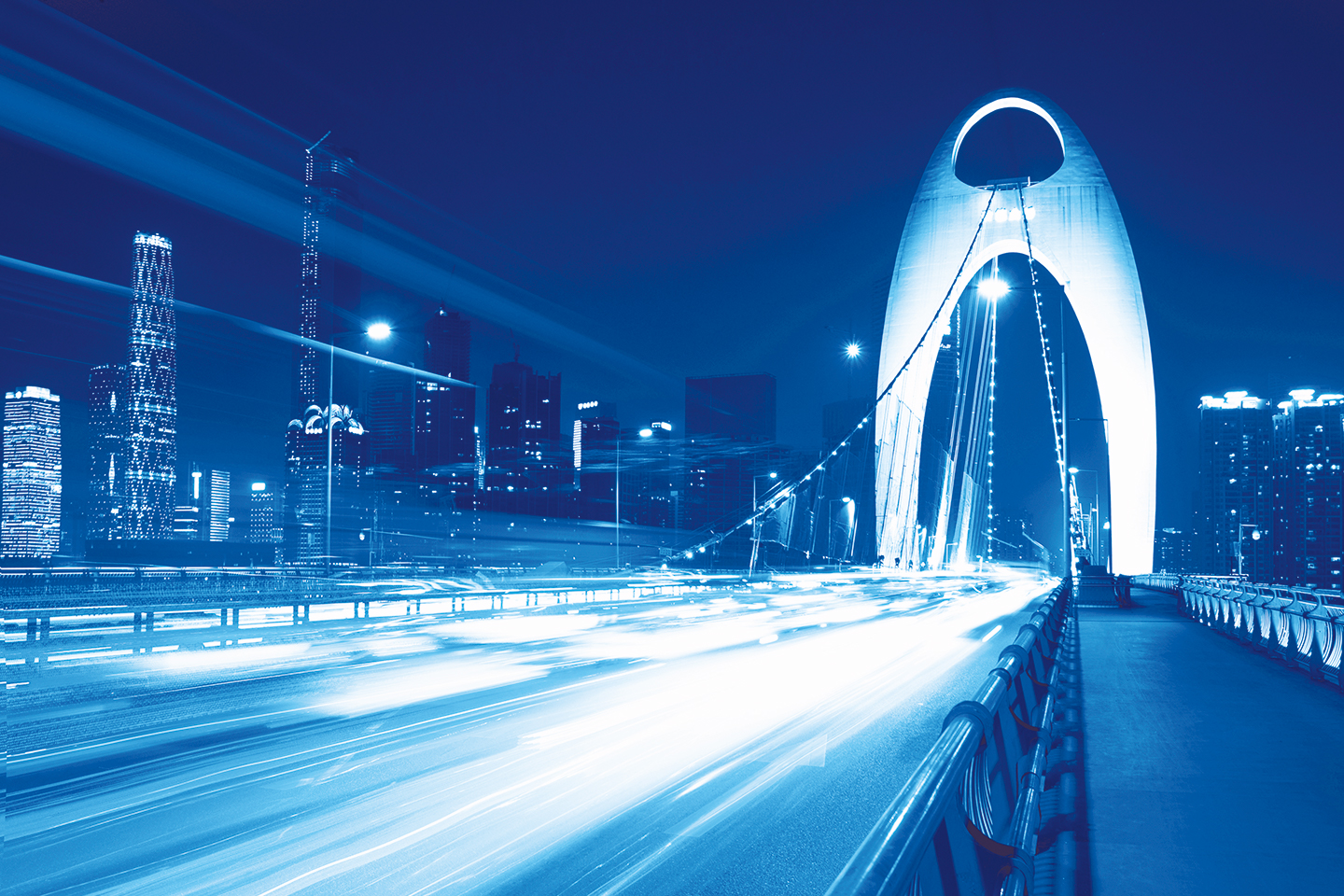
Damit Mobilität nachhaltiger gestaltet werden kann, setzen Automobilhersteller auf batterie- und brennstoffzellenbasierte Antriebe. Um die effiziente Entwicklung und Erprobung von Brennstoffzellen-Steuergeräten zu ermöglichen, bedarf es innovativer Test- und Validierungsmethoden. ETAS liefert dafür ein Gesamtpaket samt Simulationsmodellen.
Die Entwicklung brennstoffzellenbasierter Antriebe rückt sowohl in der Automobilindustrie als auch in der (Umwelt-) Politik in den Fokus und nimmt nun Fahrt auf. Denn vor allem im kommerziellen Fahrzeugbereich (Warentransport, öffentlicher Verkehr ...) hat die Brennstoffzellentechnologie große Vorteile gegenüber der rein batterieelektrischen Technologie (zum Beispiel Energiedichte oder die Lade-/Betankungszeit).
Dafür müssen Brennstoffzellen allerdings auch auf chemischer, mechanischer und elektrischer Ebene weiter reifen. Zusätzlich birgt auch ihre elektronische Regelung mit Steuergeräten noch Herausforderungen. Um diese zu lösen, sind effiziente, spezifisch auf Brennstoffzellen ausgerichtete Test- und Validierungsmethoden gefragt.
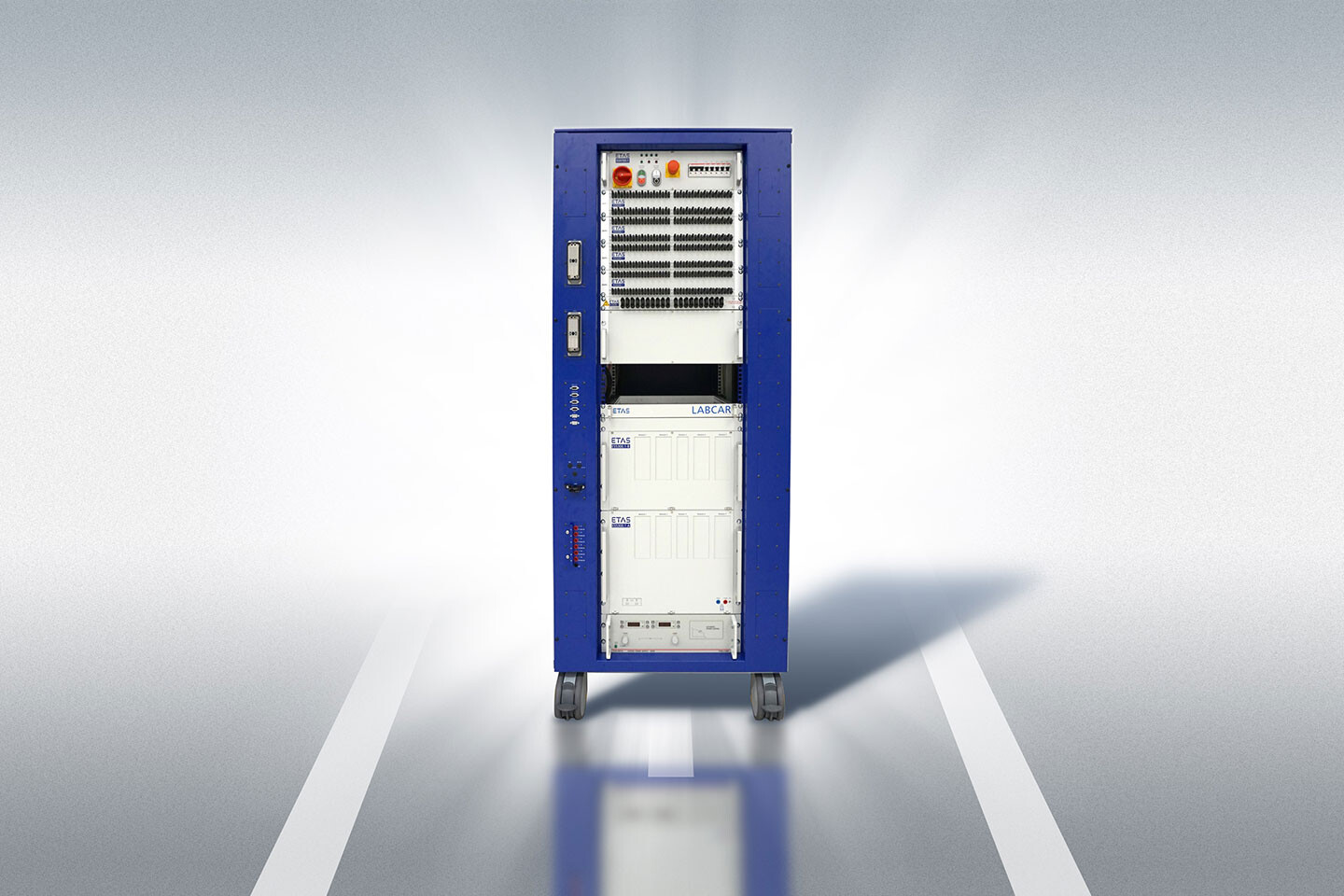
Virtualisierung unterstützt effiziente Software-Entwicklung
Das Hauptziel von HiL-Systemaufbauten ist es, den Fahrer, das Fahrzeug und seine Komponenten sowie die Umgebung so realitätsnah wie möglich und nötig zu simulieren. Die Simulationsgenauigkeit lässt sich anhand von Qualitätszielen definieren, die jeweils in Abstimmung mit den involvierten Entwicklerteams festgelegt werden. Die Virtualisierung steigert die Effizienz und sorgt für klare Zeit- und Kostenvorteile in der Software-Entwicklung, da diese schon ab der frühen Pilotphase signifikant zum Entwicklungsfortschritt beiträgt. Funktionsentwickler können damit von ihrem Schreibtisch aus sicherheitskritische Funktionen der Steuergerätesoftware testen. Dazu gehören zum Beispiel Wasserstoff-Leckage-Erkennung, Sicherheitskonzepte oder Einschalt- und Vorlade-Algorithmen elektrischer Komponenten. Die Ergebnisse können sie nahtlos in begleitende Labortests übernehmen.
Bild 1 zeigt die Frontansicht eines Brennstoffzellen-HiL-Systems. Zur Konfiguration bietet es analoge und digitale Ein-/ Ausgangs-Hardwareboards und Bus-Kommunikationsschnittstellen (CAN, LIN etc.). Zusätzlich sind wahlweise reale oder simulierte elektronische Lasten für spezielle Funktionalitäten integriert. Mithilfe eines elektronischen Injektorlast-Moduls im HiL-System lässt sich beispielsweise ein Wasserstoff-Gasinjektor hochgenau simulieren. Das Brennstoffzellenmodell ist für den Betrieb unter strikten Echtzeitbedingungen auf einem Echtzeit-Simulations-Computer ausgelegt. Dabei dient die Software-Integrationsplattform ETAS COSYM als Verbindung zwischen den Ein- und Ausgängen des physikalischen Brennstoffzellen-Simulationsmodells und den Ein- und Ausgängen der HiL-Hardware. Die Schleife zwischen Simulation, Brennstoffzellen-Software-Interaktion und dem simulierten Brennstoffzellensystem wird mithilfe der Kalibrierschnittstelle des Brennstoffzellen-Steuergeräts geschlossen.
Basis ist ein exaktes physikalisches Simulationsmodell
Kernkomponente des HiL-Systems ist das physikalische Simulationsmodell des Brennstoffzellensystems ETAS LABCARMODEL-FC. Es besteht aus fünf Hauptbestandteilen (Bild 2), die maßgeblichen Einfluss auf die Effizienz des Brennstoffzellensystems haben:
- Brennstoffzellenmodul
- Anodenpfad mit Wasserstoffversorgung/Tank
- Kathodenpfad für die Luftzufuhr
- Kühlung zur Systemtemperaturregelung
- Elektrischer Hochspannungspfad für die Energiespeicherung, Spannungsumwandlung und der elektrischen Last (Elektromotor)
Um dieses Modell auf dem HiL-System zu betreiben, müssen wichtige Voraussetzungen erfüllt sein. Das Softwaremodell muss echtzeitfähig sein. Auch ist es erforderlich, dass sich mit dem Einzelzellen-Brennstoffzellen-Modell detaillierte physikalische Zusammenhänge simulieren lassen. Beispiele hierfür sind etwa Verluste und weitere Effekte, die den elektrischen Stromfluss, die Temperatur oder die elektrische Widerstands-Stöchiometrie beeinflussen.
Einzubeziehen sind zudem die detaillierte Wasserzusammensetzung sowie zweiphasige Wassermodell-Berechnungen der Bewegungen und Aggregatzustände des Wassers im Gaskanal. Damit verbunden ist die Anforderung, die individuelle Gaskomposition an einzelnen Elektroden spezifizieren und Druckverlust-Charakteristika beschreiben zu können. Hierzu dient ein 1-D-Multikomponenten-Gaskanal-Modell.
Des Weiteren ist die Unterstützung unterschiedlicher Flussfelddesigns und die detaillierte Berechnung der internen Zellfeuchtigkeit erforderlich. Neben diesen Basisfunktionen muss eine hochgenaue Simulation das Kaltstart-Verhalten im Betrieb der Brennstoffzelle exakt nachbilden. Das setzt ein MembranTemperatur-Modell und das Einbeziehen der nichtlinearen Dynamik der Zell-Wasser-Zusammensetzung und der temperaturabhängigen Spezifika der Flüssigkeit voraus. Wünschenswert ist zudem eine Modellaufbau-Bibliothek, um das Simulationsmodell auf unterschiedliche Brennstoffzellen-Architekturen anwenden zu können.
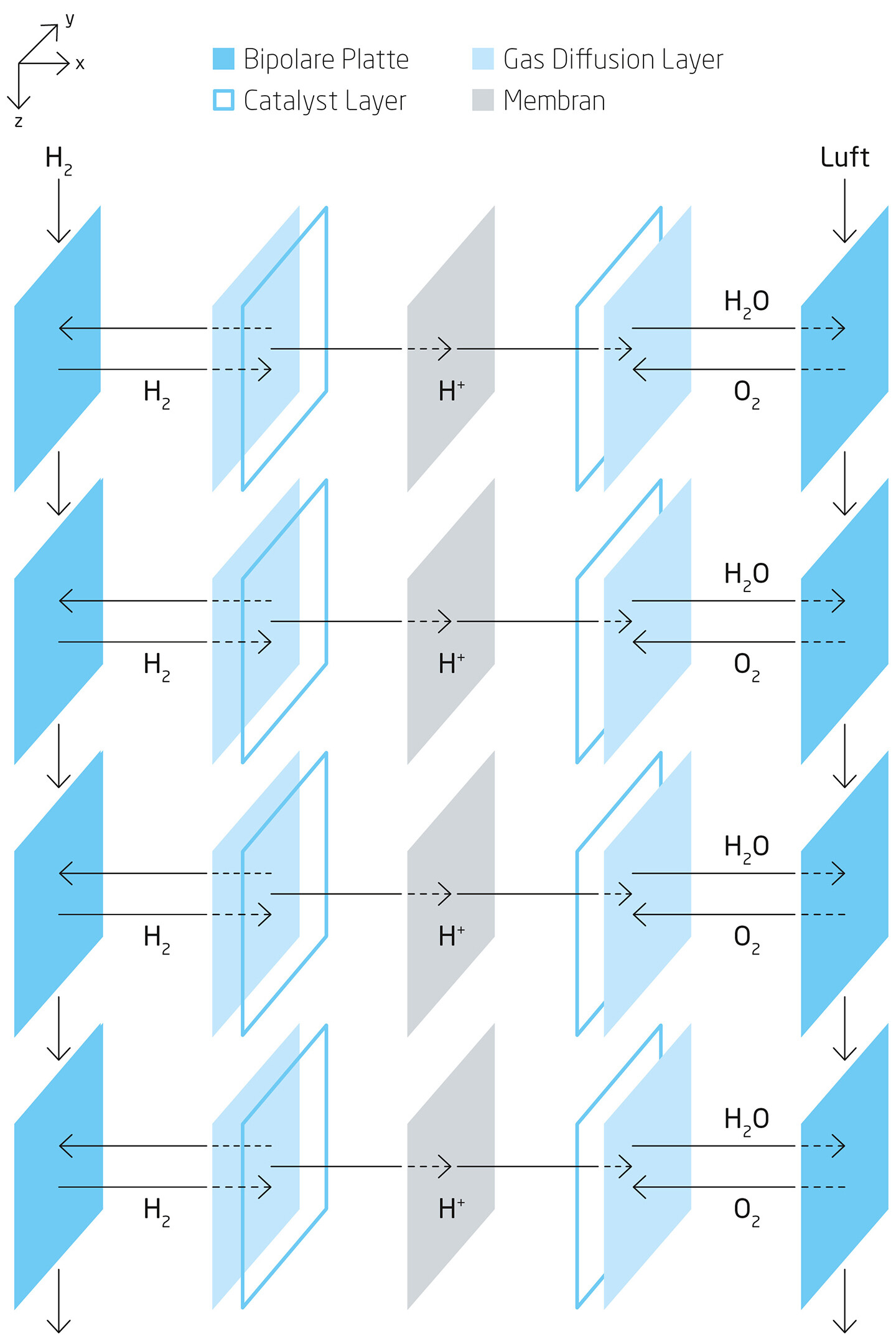
Praktikable Umsetzung
ETAS setzt diese Anforderungen systematisch um. Wie Bild 3 zeigt, lassen sich einzelne Brennstoffzellen in mehrere Segmente entlang des Gaskanals separieren. Die z-Koordinate folgt dem Gasstrom; die x- und y-Koordinaten sind senkrecht zur Membran und dem Gaskanal angeordnet. Jedes Segment erfüllt alle funktionalen Schichten der Brennstoffzelle inklusive Bipolarplatten, Gaskanälen, Gasdiffusion und Membran. So kann dasselbe Gleichungssystem für einzelne Segmente und für eine gesamte Zelle genutzt werden. Massen- und Wärmeströme verbinden die Segmente und Schichten der Zelle. Ein Austausch findet allein über den Wärme- und Massenaustausch im Gaskanal und den Bipolarplatten statt.
Dagegen trägt die Membran-Elektroden-Anordnung (MEA) kaum zum Energieaustausch mit anliegenden Segmenten bei. Auch deren Ausdehnung in x-Richtung ist um Größenordnungen kleiner als in z/y-Richtung. Räumliche Druck- und Konzentrationsgradienten, die den Protonen- und Wassertransport durch die Zelle treiben, treten daher vor allem in x-Richtung auf. Zur Modellierung der räumlichen Charakteristik genügt die Konzentration auf den Gaskanal und die Bipolarplatten. Ein solches MEA-Modell ist segmentweise auswertbar und wird vom 1-D-Modell nicht direkt beeinflusst.
Eine Komponentenbibliothek mit Wasserstoff-Gas-Injektor, Wasserstoff-Rezirkulations-Gebläse, dem Entlüftungsventil im Anodenpfad, Luftkompressor und Befeuchter im Kathodenpfad, Kühlungspumpe, MCV-Ventil im Kühlpfad, Sicherheitskreis und DCDC-Hochvolt-Eingang vervollständigt den ETAS Ansatz, der ein vollständiges Brennstoffzellen-Streckenmodell für den Einsatz im HiL-System liefert.
Anwendung
Die Leistungsfähigkeit und Genauigkeit der ETAS Lösung zeigt sich beim Vergleich zwischen einem Experiment auf einer LABCAR-HiL-Echtzeitsimulationsplattform unter Nutzung einer Basisparametrierung (Bild 4, rote Linie) und einer Fahrzeugtestfahrt (blau) mit demselben Brennstoffzellen-Steuergerät. Der Anoden(Wasserstoff)-Differenzdruck folgt exakt dem Trend der Fahrzeugtestfahrt. Die Massen-Durchflussrate der „Luft” am Verdichter weist in Testfahrt und Modell große Übereinstimmung auf. Auch die Werte des von der Brennstoffzelle abgeführten elektrischen Stroms und der Spannung stimmen sehr genau überein.
Damit ist das Potenzial der Lösung aber nicht erschöpft. Wird das Brennstoffzellenmodell im Vorfeld mit Daten aus Prüfstandversuchen kalibriert, beispielsweise mit ETAS ASCMOMOCA, ist die Simulationsgenauigkeit noch weiter optimierbar. Dafür sind im Brennstoffzellenmodell aktuell rund 350 Parameter einstellbar. Die Entwickler können so flexibel auf die Anforderungen unterschiedlicher Steuergerätesoftwareprojekte reagieren. Zudem können sie die Simulationsergebnisse durch die Integration weiterer Simulationen des E-Motors, der Batterien oder der Fahrzeugdynamik weiter verbessern.
Das Brennstoffzellen-Modell ist nicht nur für Test- und Validierung am HiL-System einsetzbar, sondern auch für virtuelle Testabläufe im Frühstadium der Software-Entwicklung. Dabei erlaubt die ETAS XiL-Testplattform COSYM neben der Validierung der Softwarefunktionen im Closed-Loop-Experiment auch die Integration des Simulationsmodells in ein gleichfalls simuliertes, übergeordnetes Fahrzeugmodell. Die Nachbildung sämtlicher Fahrzeugbusse – ob virtuelle CAN- oder Automotive-Ethernet-Netzwerke – ermöglicht es den Entwicklern, die Netzwerkkommunikation schon in diesem Stadium realitätsnah zu analysieren.
Fazit
Sicherheit, Leistungsfähigkeit und Überwachung der Antriebskomponenten bleiben wichtige Zielgrößen der Entwicklung elektrifizierter Antriebskomponenten. Gerade bei der Neu- und Weiterentwicklung von Brennstoffzellen-Steuergeräten liefern präzise Echtzeitsimulationen der Brennstoffzelle die Grundlage für die Validierung auf den HiL-Prüfständen. Der Einsatz von SiL-Testplattformen erlaubt zudem schon ab dem Frühstadium der Entwicklung begleitende Tests. Mit der vorliegenden XiL-Lösung samt Simulationsmodellen liefert ETAS die Basis für eine hocheffiziente und rundum sichere Entwicklung von Brennstoffzellen-Steuergeräten. Damit kommt die Brennstoffzelle dem Großserieneinsatz in klimafreundlichen Fahrzeugen der Zukunft einen weiteren Schritt näher.
Autoren
Frank Ruschmeier ist Application Field Manager Test and Validation bei der ETAS Automotive Technology Co., Ltd.
Chaoyong Tang ist Program Manager Test and Validation Fuel Cell bei der ETAS Automotive Technology Co., Ltd.
Raphael Hans ist Test and Validation Modeling Specialist und Fuel Cell Expert bei der ETAS GmbH.
Weitere Informationen
LABCAR-MODEL
-
Herausforderung „Antrieb der Zukunft“ Download